RTM is a team of young and enthusiastic employees who have earned their stripes in the (radio)pharmaceutical industry, science and medical imaging. This team is led by Lars Perk. As Managing Director of RTM he was also in charge of the layout and inventory of the RTM laboratories. The doors opened in august 2015 and the 1200 square meters of this facility give room to a wide range of Von Gahlen installations. This range helps RTM to develop, prepare and distribute radiopharmaceuticals. Together with Arnod Busser, Area Sales Manager at Von Gahlen, Lars reviews this large-scale project.
PET tracer productions in optimal daylight
“Our facility houses three Von Gahlen hot cell suites, connected to a cyclotron with an Activity Distribution System”, as Lars illustrates. “In these production rooms (i.e., clean rooms or GMP-labs) we produce PET tracers, mainly 18F-labeled. In smaller volumes we also produce 89Zr-labeled antibodies and process 166Ho-labeled microspheres. The latter is the only therapeutic compound that leaves our facility. All our other productions are purely for diagnostics purposes.”
Arnod points out the huge glass walls surrounding the hot cell suites. “That’s not something you see every day. Even the cyclotron control room has a skylight.” Lars explains why: “We wanted to create spacious rooms with lots of daylight to offer a healthy working space for our employees. This criterion was very well executed by the architect and the builders. Rooms like these used to be heavily bunkered back in the days, but that’s not necessary anymore. Nowadays, radiation safety doesn’t mean you have to sacrifice daylight.”
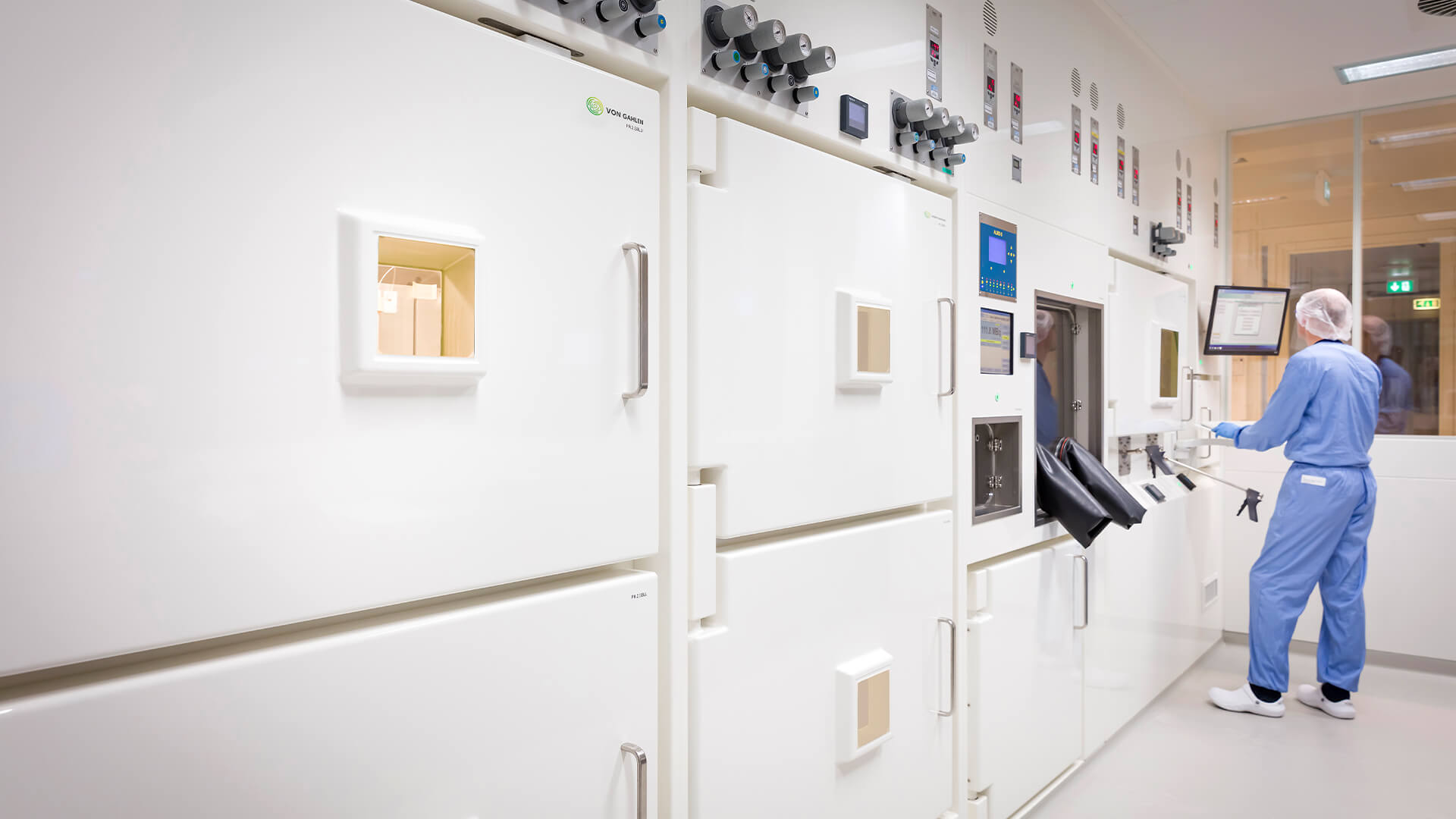
One of the three hot cell suites at RTM
Additional equipment to complete the picture
All that transparency reveals more Von Gahlen products. Two semi-automatic open vial dose dividers complement the hot cells. The RTM building accommodates Quality Control labs containing two Shielded Fume Hoods for quality controls and preparations of samples and tests. There is also a (non-GMP) lab with a research hot cell and two more Shielded Fume Hoods. All this additional equipment was built and installed by Von Gahlen.
A diligent tendering process
Prior to that, a European tender took place. In 2014 Von Gahlen was selected as supplier and Lars reflects on that tendering process. “Pricing was an obvious factor, but next to that, suppliers were ranked via a points system for certain quality criteria. This system, together with how long suppliers have been in business and whether or not they work with a quality system, were also factors we took into account. On all these criteria Von Gahlen scored the highest points, making them our supplier.”
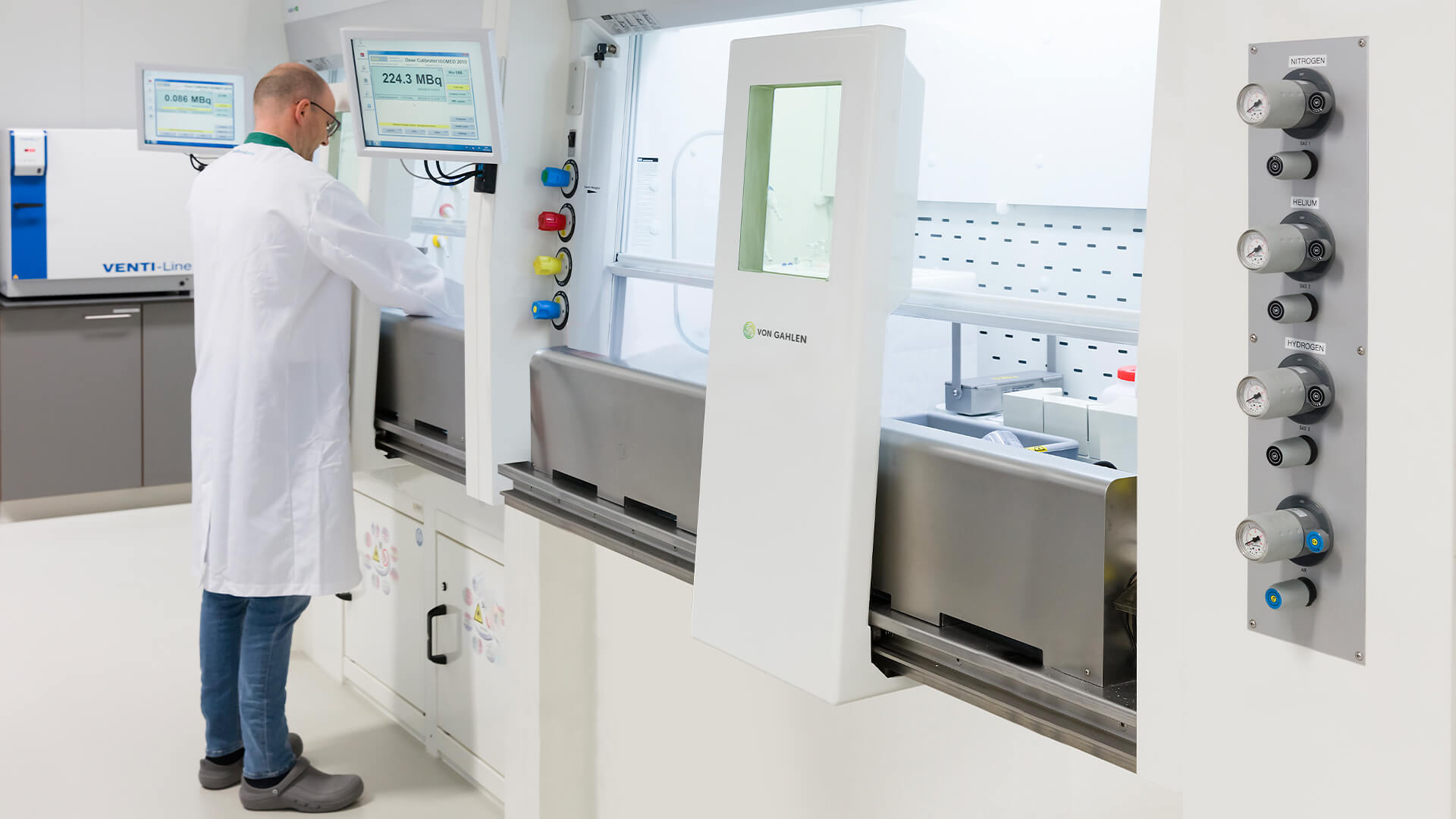
Shielded Fume Hoods in action
Solid and sound
When asked to characterize Von Gahlen, Lars mentions one thing in particular: “It’s a real family business. Through years you keep seeing the same familiar faces, which basically means that long term employments are no exceptions at Von Gahlen. The organization is solid and sound and my colleagues and I have direct lines of contact to whomever we need within the Von Gahlen organization. Whether it’s Jaap or Alex (Managing Directors, red.), Theo the Project Manager or Anja from the service department.”

A semi-automatic open vial dose divider (OVDD-SA) at RTM
A steady production increase
It was only five years ago that Von Gahlen had finalized their equipment installation at RTM. In just one year RTM managed to get their GMP-certificate and to start production. RTM has been steadily increasing its production volume ever since. Approximately one third of this volume goes to Radboudumc. The rest is being distributed to several customers and to nearby hospitals, mainly in the eastern region of The Netherlands. “And we have serious plans for a second cyclotron”, anticipates Lars ambitiously. Arnod concludes the story by expressing his admiration for the RTM building: “It’s simply a beautiful facility in which every detail is very well thought out. It really appeals to one’s imagination, not only to people in nuclear medicine. The last couple of years, if we wanted to give people a good and comprehensive impression of what Von Gahlen does, we visited RTM. So we have to thank Lars for his hospitality.”
And so we do for this interview as well. It has been a wonderful project on which we look back proudly and gratefully.
If you have similar needs for your laboratory, please do not hesitate to discuss the possibilities with us.