Still going strong
Back in 2008, Helse Bergen Haukeland University Hospital established a radiopharmacy for PET radiopharmaceuticals and PET research. “We equipped this radiopharmacy with a mixture of hot cells for regulated production in a GMP environment and for research & development”, says Tom. “Today, twelve years later, this equipment still meets the current needs of the hospital and our department. Perhaps future needs might require additional synthesis hot cells or dispenser hot cells.”
Von Gahlen was selected in a tender process. This was the start of a project in which Tom and the Von Gahlen project team closely collaborated. Or as Tom recalls: “I remember how timely and well their planning for this big project was. They saw our needs and added input to solutions during the planning phase. And ever since the installation, the hot cells have been performing as expected.”
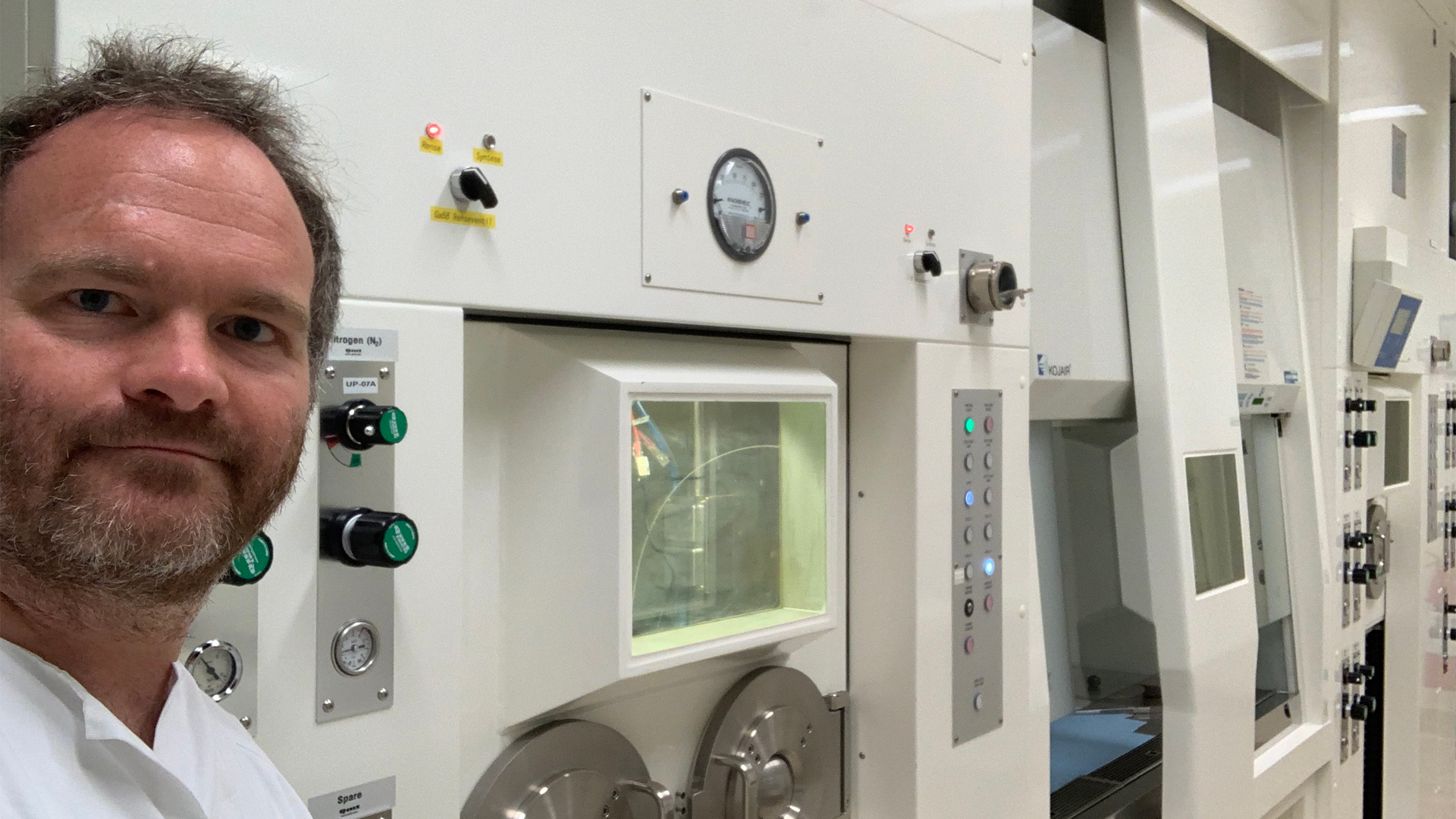
Tom Christian Holm Adamsen in front of the twelve-year-old hot cells at Helse Bergen Haukeland University Hospital
Avoiding unplanned downtime
The long-term endurance of a hot cell is not a complete coincidence. Helse Bergen Haukeland University Hospital decided to setup and sign a service agreement with Von Gahlen, to optimize the lifecycles of the installation. Tom explains the content of such an agreement. “Our service agreement includes spare parts and a yearly visit by a service engineer. He checks the functionality of the hot cells, changes filters and reports any issues that might require follow up, extra maintenance or correction.”
Tom is clear on why such an agreement is helpful to them. “For us as the regional and local supplier of PET-radiopharmaceuticals, downtime is something we strive to prevent. Preventive maintenance is essential to avoid unplanned downtime and to be compliant towards the authorities (GMP). If these kind of services would lack, it could mean more frequent downtime and disruption in the production. For the hospital this would mean lower quality of patient care.”
Benefit from the Von Gahlen services
Obviously, we are excited to see our products facilitating such important work at this fantastic hospital. Especially when this equipment has been doing so for more than twelve years now. We thank Tom for sharing his experiences with the Von Gahlen services.
Please feel free to contact us if you would like to know more about our lifecycle optimization services.
Would you like to know more about this project? Or do you want to know what we could provide for you?
Feel free to contact us.